Have you ever faced a problem that seemed impossible to solve? As an entrepreneur and digital marketer, I’ve encountered my fair share of head-scratchers. But fear not! I’m here to introduce you to a powerful problem-solving methodology that’s been a game-changer for me:
8D Problem Solving.
This approach has helped me tackle complex issues in my business, and I’m excited to share it with you.
8D, which stands for “Eight Disciplines,” is a systematic method for identifying, correcting, and eliminating recurring problems. It’s like having a trusty Swiss Army knife for your brain, equipped with all the tools you need to dissect and resolve even the most stubborn issues.
In this blog post, we’ll dive deep into the world of 8D Problem Solving. I’ll guide you through each discipline, share real-world examples, and provide actionable tips to help you master this technique.
What is 8D Problem Solving?
8D Problem Solving is a structured, team-oriented approach to solving complex problems. It’s like a treasure map that guides you through eight specific steps (or “disciplines”) to find the root cause of an issue and implement a lasting solution.
The beauty of 8D lies in its versatility. While it was originally developed for manufacturing, I’ve found it incredibly useful in various aspects of my business, from improving customer service to streamlining marketing processes.
At its core, 8D is about digging deep, thinking critically, and working collaboratively. It’s not just about putting out fires; it’s about preventing them from igniting in the first place.
The Origins of 8D
The 8D methodology has quite an interesting history. It was first introduced by the Ford Motor Company in the 1980s as part of their “Team Oriented Problem Solving” (TOPS) program. Originally, it was called “8D” because it consisted of eight steps, all starting with the letter ‘D’.
Ford developed this approach to help improve product quality and address recurring issues in their manufacturing processes. However, the roots of 8D can be traced back even further to the U.S. government’s Military Standard 1520 (Corrective Action and Disposition System for Nonconforming Material), which was issued during World War II.
Over time, 8D has evolved and been adapted by various industries beyond automotive manufacturing. Today, it’s used in healthcare, software development, and even in small businesses like mine. Its enduring popularity is a testament to its effectiveness in solving complex problems across diverse fields.
The 8 Disciplines Explained
Now, let’s break down each of the eight disciplines. Think of these as your problem-solving superpowers:
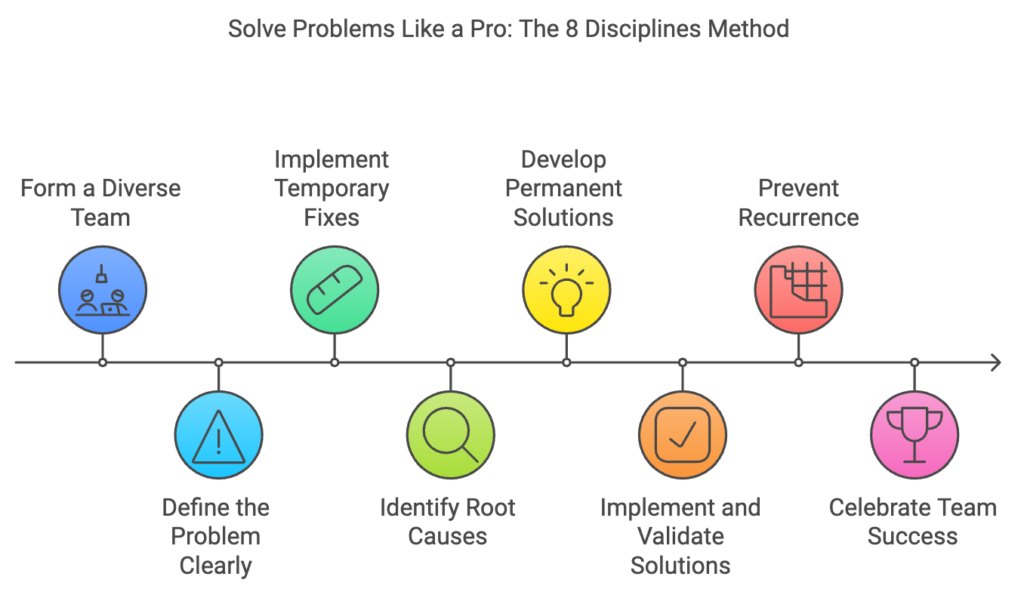
- D1: Form the Team – Assemble a group of people with diverse knowledge and skills related to the problem. In my experience, having different perspectives is crucial for finding innovative solutions.
- D2: Define the Problem – Clearly describe the issue using specific terms. I always ask, “What’s happening that shouldn’t be happening, or what’s not happening that should be?”
- D3: Implement Interim Containment Actions – Put temporary fixes in place to minimize the problem’s impact until a permanent solution is found. This is like applying a bandage before treating the wound.
- D4: Identify and Verify Root Causes – Dig deep to find the underlying causes of the problem. I love using the “5 Whys” technique here.
- D5: Develop Permanent Corrective Actions – Create long-term solutions that address the root causes identified in D4.
- D6: Implement and Validate Corrective Actions – Put your solutions into action and verify that they work. This is where the rubber meets the road!
- D7: Prevent Recurrence – Modify systems and processes to ensure the problem doesn’t happen again. It’s about building fences at the top of the cliff, not parking ambulances at the bottom.
- D8: Congratulate the Team – Recognize the efforts of everyone involved. In my company, we always celebrate our problem-solving wins, no matter how small.
When to Use 8D Problem Solving
8D Problem Solving isn’t a one-size-fits-all solution. It’s most effective when dealing with complex, recurring issues that require a team effort to resolve. Here are some scenarios where I’ve found 8D to be particularly useful:
- When facing persistent quality issues in product development
- Addressing recurring customer complaints
- Tackling operational inefficiencies that impact multiple departments
- Resolving conflicts between different teams or stakeholders
- Improving safety procedures after a workplace incident
Remember, 8D is a comprehensive approach that requires time and resources. For simple, straightforward problems, a less intensive method might be more appropriate. It’s all about matching the tool to the task!
Benefits of 8D Problem Solving
Implementing 8D Problem Solving can bring numerous advantages to your organization. Here are some key benefits I’ve experienced:
- Structured Approach: 8D provides a clear roadmap for problem-solving, ensuring no crucial steps are missed.
- Root Cause Analysis: By focusing on identifying the root cause, 8D helps address the underlying issue, not just the symptoms.
- Team Collaboration: The methodology encourages cross-functional teamwork, fostering better communication and knowledge sharing.
- Continuous Improvement: 8D promotes a culture of ongoing learning and process enhancement.
- Documentation: The process creates a valuable record of problems and solutions, which can be referenced in the future.
- Customer Satisfaction: By effectively resolving issues, 8D can lead to improved product quality and customer experience.
- Cost Reduction: Preventing recurring problems can result in significant cost savings over time.
Common Pitfalls and How to Avoid Them
While 8D is a powerful tool, it’s not without its challenges. Here are some common pitfalls I’ve encountered and how to sidestep them:
- Rushing the Process: Take the time to thoroughly complete each step. Skipping or rushing stages often leads to incomplete solutions.
- Lack of Team Diversity: Ensure your team includes members from various departments and with different expertise levels.
- Focusing on Blame: Remember, the goal is to solve the problem, not to point fingers. Foster a blame-free environment.
- Overlooking Data: Base your decisions on facts and data, not assumptions or hunches.
- Neglecting Follow-up: Don’t forget to monitor the implemented solutions to ensure they’re effective in the long term.
- Poor Documentation: Keep clear, detailed records throughout the process. This information is invaluable for future reference.
- Resistance to Change: Be prepared to challenge the status quo and implement significant changes if necessary.
By being aware of these potential stumbling blocks, you can navigate the 8D process more smoothly and achieve better results.
8D Problem Solving in Action: A Case Study
Let me share a real-world example of how a digital marketing agency used 8D Problem-Solving. They were facing a recurring issue with missed deadlines on client projects, leading to dissatisfaction and potential loss of business.
Here’s how they applied the 8D methodology:
- D1: Form the Team: They assembled a cross-functional team including project managers, content creators, designers, and account managers.
- D2: Define the Problem: They clearly stated the issue: “30% of client projects are being delivered past the agreed deadline, resulting in a 15% decrease in client satisfaction scores.”
- D3: Implement Interim Containment Actions: They temporarily increased their workforce by hiring freelancers to help clear the backlog of projects.
- D4: Identify and Verify Root Causes: Through root cause analysis, they discovered that:
- Project scopes were often poorly defined at the outset
- There was a lack of standardized processes across different project types
- Communication breakdowns were occurring between team members
- D5: Develop Permanent Corrective Actions: They decided to:
- Implement a standardized project scoping process
- Develop and document clear workflows for each type of project
- Introduce a project management tool to improve team communication
- D6: Implement and Validate Corrective Actions: They rolled out these changes over a three-month period, closely monitoring project delivery times and client satisfaction scores.
- D7: Prevent Recurrence: They established regular training sessions on the new processes and tools, and implemented a monthly audit of project timelines.
- D8: Congratulate the Team: They celebrated success with a team dinner and recognized key contributors in the company newsletter.
The result? Within six months, on-time project delivery rate improved to 95%, and client satisfaction scores increased by 25%. This case study demonstrates the power of the 8D methodology when applied systematically and thoroughly.
Tools and Templates for 8D Problem Solving
To make your 8D journey smoother, here’s a table summarizing some useful tools and templates for each discipline:
Discipline | Tools and Templates |
---|---|
D1: Form the Team | Team Charter Template, Skills Matrix |
D2: Define the Problem | Problem Statement Worksheet, Is/Is Not Analysis |
D3: Implement Interim Containment Actions | Containment Action Plan Template |
D4: Identify and Verify Root Causes | Fishbone Diagram, 5 Whys Template |
D5: Develop Permanent Corrective Actions | Solution Selection Matrix, Action Plan Template |
D6: Implement and Validate Corrective Actions | Implementation Checklist, Validation Plan Template |
D7: Prevent Recurrence | Process FMEA, Control Plan Template |
D8: Congratulate the Team | Recognition Plan Template, Lessons Learned Document |
These tools can help streamline your 8D process and ensure you’re covering all bases at each step. Remember, the key is to adapt these tools to fit your specific needs and organizational culture.
Integrating 8D with Other Problem-Solving Methods
While 8D is a powerful methodology on its own, I’ve found that integrating it with other problem-solving approaches can lead to even better results. Here are a few methods that complement 8D nicely:
- Six Sigma: This data-driven approach to process improvement works well with 8D, especially in the root cause analysis and solution validation stages.
- Lean Thinking: Lean principles can enhance 8D by focusing on eliminating waste and improving efficiency throughout the problem-solving process.
- Design Thinking: This human-centered approach can be particularly useful in the early stages of 8D, helping to define the problem from the user’s perspective.
- PDCA (Plan-Do-Check-Act): This iterative approach aligns well with 8D’s emphasis on continuous improvement.
- TRIZ (Theory of Inventive Problem Solving): TRIZ can provide innovative solutions during the corrective action development stage of 8D.
By combining these methodologies, you can create a robust, flexible problem-solving framework that adapts to various situations and challenges.
Building a Culture of Problem Solving
Implementing 8D Problem Solving isn’t just about following a set of steps; it’s about fostering a culture where everyone in the organization is empowered to identify and solve problems. Here are some strategies I’ve used to build this culture:
- Lead by Example: As a leader, I make sure to use 8D principles in my own decision-making processes and communicate this to my team.
- Provide Training: Offer regular workshops and training sessions on 8D and other problem-solving techniques.
- Encourage Participation: Create opportunities for employees at all levels to participate in problem-solving teams.
- Reward Initiative: Recognize and reward individuals and teams who proactively identify and solve problems.
- Create Safe Spaces: Foster an environment where people feel safe to raise issues and propose solutions without fear of blame.
- Share Success Stories: Regularly communicate how 8D has been used to solve problems and improve processes within the organization.
- Integrate into Performance Reviews: Include problem-solving skills as a key component in employee evaluations and development plans.
Remember, building this culture takes time and consistent effort, but the payoff in terms of organizational resilience and continuous improvement is well worth it.
8D Problem Solving in the Digital Age
As we navigate the digital age, 8D Problem Solving is evolving to meet new challenges. Here’s how I’ve seen 8D adapt to the digital landscape:
- Virtual Teams: With remote work becoming more common, 8D teams are often distributed across different locations. Digital collaboration tools are essential for effective teamwork.
- Data Analytics: Big data and advanced analytics are transforming how we identify problems and verify root causes in 8D.
- AI and Machine Learning: These technologies can help predict potential issues before they occur, enhancing the preventive aspect of 8D.
- Digital Documentation: Cloud-based platforms allow for real-time, collaborative documentation of the 8D process, improving transparency and knowledge sharing.
- Simulation Tools: Digital simulations can help test potential solutions before implementation, reducing risk and improving outcomes.
- IoT Integration: Internet of Things (IoT) devices can provide real-time data for monitoring and problem detection, making the 8D process more proactive.
By embracing these digital tools and trends, we can make 8D even more powerful and responsive to today’s fast-paced business environment.
Measuring the Success of 8D Implementation
To ensure that your 8D problem-solving efforts are truly making a difference, it’s crucial to measure their impact. Here are some key performance indicators (KPIs) I use to gauge the success of 8D implementation:
- Problem Recurrence Rate: This measures how often similar problems occur after implementing 8D solutions. A lower rate indicates more effective problem-solving.
- Time to Resolution: Track how long it takes to resolve issues using the 8D method. Over time, this should decrease as your team becomes more proficient.
- Cost Savings: Calculate the financial impact of problems solved through 8D, including both direct costs and opportunity costs.
- Customer Satisfaction Scores: Monitor how customer satisfaction changes in relation to 8D problem-solving efforts.
- Employee Engagement: Measure how involvement in 8D processes affects employee satisfaction and engagement levels.
- Number of Preventive Actions: Track the number of preventive measures implemented as a result of 8D analyses.
- Quality Metrics: Monitor relevant quality indicators in your industry to see how they improve with 8D implementation.
Remember, the goal isn’t just to solve problems, but to create lasting improvements in your processes and outcomes.
The Future of 8D Problem Solving
As we look ahead, I see several exciting trends shaping the future of 8D Problem Solving:
- Integration with AI: Artificial Intelligence could revolutionize how we approach each discipline, from problem identification to solution generation.
- Predictive Problem Solving: Advanced analytics may allow us to anticipate and address issues before they even occur, shifting 8D from reactive to proactive.
- Augmented Reality in Problem Solving: AR could provide new ways to visualize problems and solutions, especially in manufacturing and engineering contexts.
- Blockchain for Transparency: Blockchain technology could enhance the documentation and verification aspects of 8D, ensuring the integrity of the problem-solving process.
- Personalized Problem-Solving Approaches: Machine learning algorithms could help tailor the 8D process to specific industries, organizations, or even individual problem-solvers.
- Global Collaboration Platforms: As organizations become more global, we’ll see the rise of platforms designed specifically for international 8D teams to collaborate effectively.
- Integration with Sustainability Goals: 8D may evolve to explicitly consider environmental and social impacts in its problem-solving framework.
These developments promise to make 8D even more powerful and adaptable in the years to come. The key will be to embrace these innovations while maintaining the core principles that make 8D so effective.
Q&A
Q1: How long does a typical 8D process take?
A1: The duration of an 8D process can vary greatly depending on the complexity of the problem. Simple issues might be resolved in a few days, while more complex problems could take weeks or even months. The key is to be thorough rather than rushed.
Q2: Can 8D be used for personal problem-solving?
A2: Absolutely! While 8D was designed for organizational use, its principles can be adapted for personal problem-solving. The structured approach and emphasis on root cause analysis can be particularly helpful for addressing persistent personal challenges.
Q3: How is 8D different from other problem-solving methods like PDCA or Six Sigma?
A3: While there are similarities, 8D is more structured and team-oriented than PDCA. Compared to Six Sigma, 8D is less statistically driven and can be implemented more quickly. However, these methods can complement each other well when used together.
Q4: Is special software required to implement 8D?
A4: While there are software tools designed specifically for 8D, they’re not necessarily required. Many organizations successfully implement 8D using general-purpose tools like spreadsheets, project management software, or even pen and paper.
Q5: How can I convince my organization to adopt 8D Problem Solving?
A5: Start by highlighting the benefits, such as improved quality, cost savings, and increased customer satisfaction. You might also consider running a pilot project to demonstrate its effectiveness. Sharing success stories from other organizations in your industry can also be persuasive.
8D Problem Solving Quiz
Test your understanding of 8D Problem Solving with this quick quiz:
- The “D” in 8D stands for: a) Directions b) Disciplines c) Dimensions d) Developments
- Which discipline involves putting temporary fixes in place? a) D2 b) D3 c) D4 d) D5
- Root cause analysis is primarily addressed in which discipline? a) D3 b) D4 c) D5 d) D6
- The final discipline (D8) focuses on: a) Implementing solutions b) Preventing recurrence c) Congratulating the team d) Documenting the process
- 8D Problem Solving originated in which industry? a) Software development b) Healthcare c) Automotive manufacturing d) Aerospace
Answers:
- b) Disciplines
- b) D3
- b) D4
- c) Congratulating the team
- c) Automotive manufacturing
Scoring:
- 5 correct: You’re an 8D expert! You’re well-equipped to lead problem-solving initiatives.
- 3-4 correct: Good understanding of 8D. With a bit more practice, you’ll be solving problems like a pro.
- 1-2 correct: You’re on the right track. Review the 8D process and try again.
- 0 correct: Time to dive back into the article! 8D can be complex, but with some study, you’ll get there.
In conclusion, 8D Problem Solving is a powerful tool that can transform how you and your organization approach complex issues. By following this structured method, fostering a culture of problem-solving, and staying adaptable in the face of technological changes, you can turn challenges into opportunities for growth and improvement.